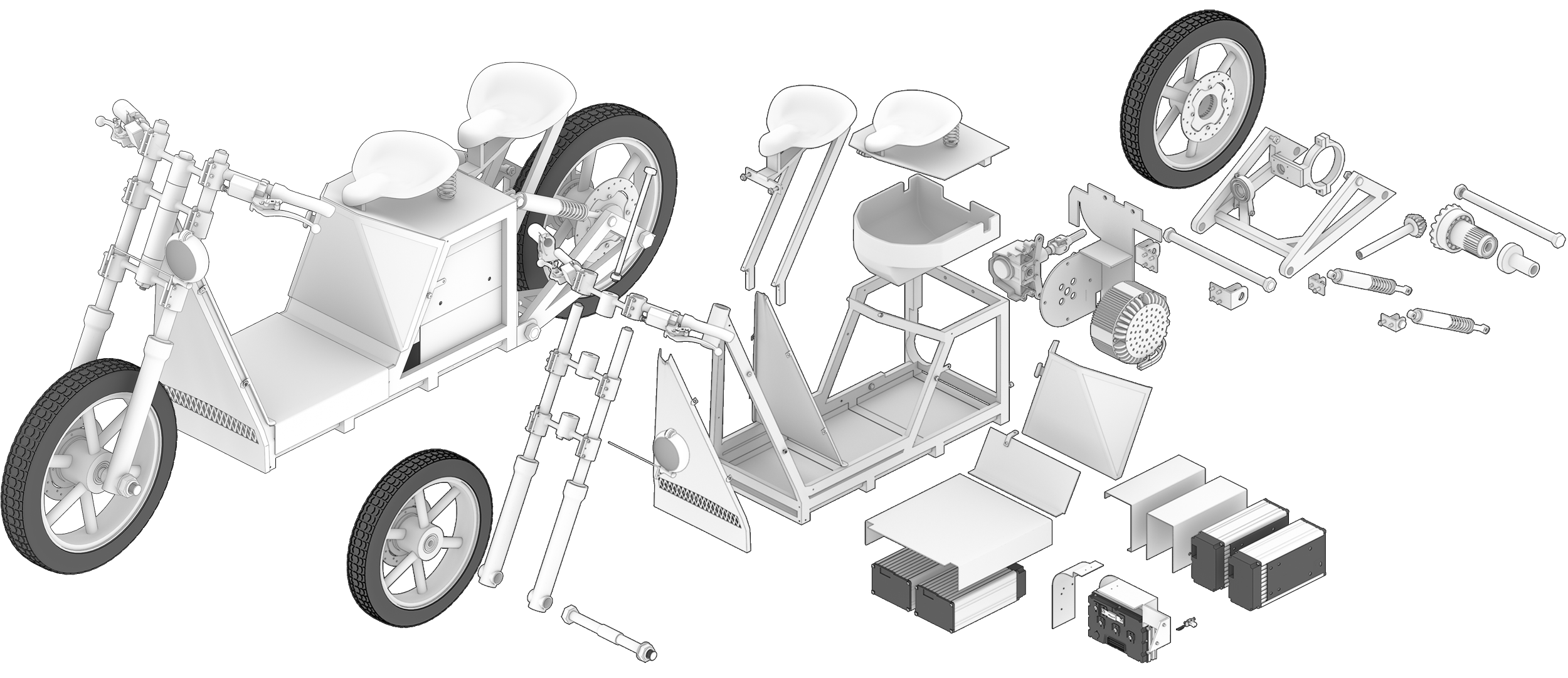
Goal
The Mahjouba II installation requires documentation and visualisations to showcase its interior design and assembly to the general public at the Design Museum in London. As a guiding aesthetic, 3D components and exploded renders should emulate the minimalistic style used in IKEA installation manuals.
Context
Mahjouba II is the second of a series of prototypes to build an electric motorbike made primarily using African craft in combination with 3D printing for the Moroccan market.
A primary goal for this design is that it can be domestically built and inexpensively maintained using only craft components or readily available “off-the-shelf” parts. This prototype aims to deliver a more robust and cheaper 2-seater counterpart to the original prototype, making use of less stringent road regulations for light electric transport.
Constraints
Prototype Availability: The motorbike is owned by the London Design Museum awaiting display. There is only a weekend available to disassemble the model for reference photography and measurement.
Non-photorealism: visualisations should continue to use the instruction manual NPR aesthetic developed in the original project.
Criteria
Visual Appeal: A good design should be aesthetically pleasing whilst maintaining a clear and consistent aesthetic across all output.
Accuracy: Good renders will represent each component's dimensions and how they fit together, as faithfully to the prototype as possible.
Simplicity: Visualisations should clearly showcase how the prototype is assembled to as wide of an audience as possible.
Flexibility: All output could be used across a wide variety of mediums including posters, leaflets and instruction manuals with reduced colour palettes.
The construction process was fully documented to aid creating supplementary materials.
All components were photographed in an isometric perspective.
The Mahjouba II installation in London, 2018.
All hard-surface modelling and assembly designed within Modo 15.
To improve feedback lead times, a new process was adopted where the client could draw and comment on early development renders. Instead of discrete feedback rounds, the client could annotate feedback overnight.
The composition continued to be built from the same Final Colour and Ambient Occlusion render passes alongside a post-drop shadow to add a silhouette line. Ambient Occlusion range was increased to soften the overall style.
A total of 28 individual components were modelled.
Various exploded assembly designs.
Complete exploded design.
Project Lead Time: 2 months.
Tools Used: Modo, Photoshop.
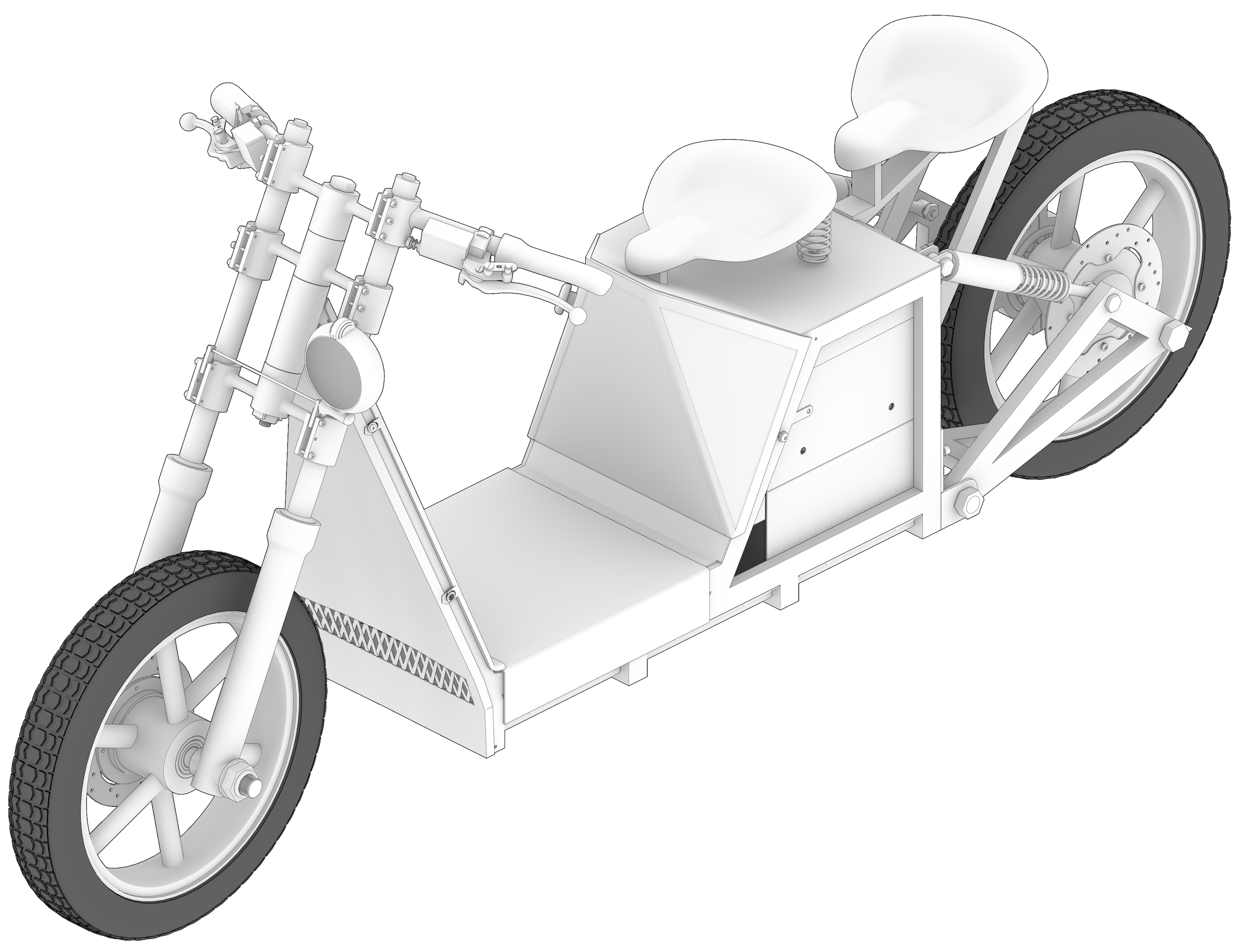